
INDUSTRY SOLUTIONS
Semiconductors & electronics
Innovative machines and technologies have made significant progress in the semiconductor industry in recent years. These machines play a critical role in producing advanced and high-performance semiconductor components used in a wide range of electronic devices, from smartphones and computers to industrial applications.
A key aspect of innovation lies in the progressive miniaturization and precision of semiconductor component manufacturing. State-of-the-art machines use sophisticated manufacturing processes such as wet chemical processes, which make it possible to create tiny circuits on semiconductor chips. These processes allow manufacturers to produce semiconductors with higher power density and efficiency.
Overall, innovative machines in the field of semiconductor production are not only technological masterpieces, but also decisive drivers for progress and innovation in almost all areas of modern life in which electronics play a role. Their influence is fundamental for the further development of technologies and for the improvement of electronic products that shape our everyday lives.

Overall, innovative machines in the field of semiconductor production are not only technological masterpieces, but also decisive drivers for progress and innovation in almost all areas of modern life in which electronics play a role. Their influence is fundamental for the further development of technologies and for the improvement of electronic products that shape our everyday lives.

Process equipment suitable for ISO 8 to ISO 4 cleanroom classes.
Compliance with these requirements is essential to ensure that the products manufactured are free of contaminants and of the highest quality.
In order to meet the requirements, our production machines have been specially designed for these types of clean rooms.
They are characterized by the following points:
Minimum particle release: The equipment is made from the highest quality materials (PFA, PVDF ECTFE but also PP or stainless steel possible), which have extremely low particle release. Additionally, any processes or movements within the equipment must be designed to release minimal contaminants into the surrounding air.
Hermetic construction: Depending on customer requirements, the equipment is hermetically sealed and equipped with filter mats or filter fan units. This prevents contamination from entering from outside.
Customization according to customer requirements: Our equipment is modular and configured according to customer requirements. This means that customer-specific process steps can be integrated quickly and easily at any time.
Modular construction: Thanks to the innovative modular design, installation times in the clean room can be minimized. All of our equipment can be installed within 3 weeks and can usually be handed over to production after just 5 weeks.
Space requirements / foot print: All of our equipment is specifically configured to customer requirements and perfectly adapted with the help of our simulation software. This means that the equipment requires 30-40% less space in the cleanroom.
Software: With the software and visualization we have developed, we are a global leader in offering the best possible flexibility through “on the fly” product changes as well as optimal product quality through substrate-based evaluations, which are made available at the SECS / GEM or OPC UA interfaces.

Desmear – High-end cleaning system as a new innovative industry standard in cleanroom production for the production of high-end IC substrates.
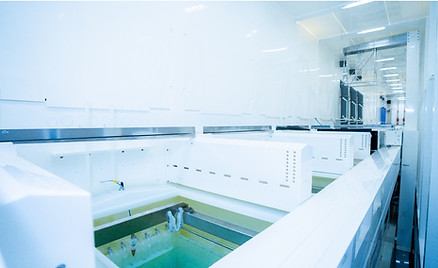

Eless Copper Plating
Electroless copper plating is a chemical process in which a very thin and uniform layer of copper is applied to the surface of a substrate.
The metal cations in the solution are reduced to metal by an autocatalytic reaction.
This creates a uniform copper metal layer during electroless plating, regardless of the geometry of the surface.


ENEPIG process
ELECTROLESS NICKEL -
ELECTROLESS PALADIUM - IMMERSION GOLD
In order to optimize the solubility or bondability of the substrates, a corrosion-free final surface must be ensured for high-end applications.
The combination of electroless processes (nickel and palladium) and the final gold plating offers an optimal solution for this.
A palladium layer is used as an oxidation barrier to prevent oxidation or corrosion of the nickel layer.

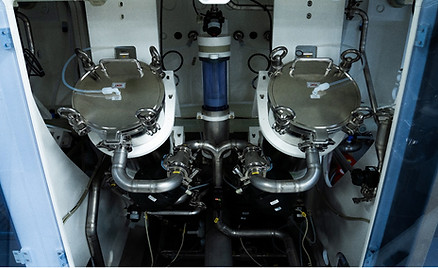
Cleaning solution

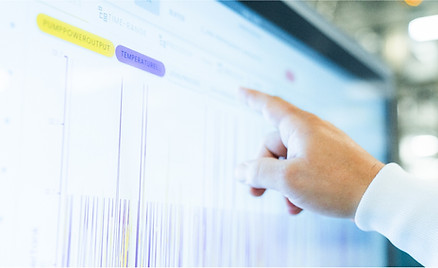
Operating concept
Our innovative operating concept offers the user a unique, intuitive and user-friendly interaction option.
